中小企业数字化转型案例12 江苏振华海科装备科技股份有限公司 基于“制造云平台一体化管控”的先进管理模式 推动企业工业互联网平台建设
时间:2022-03-29
一、案例简介
江苏振华海科装备科技股份有限公司(以下简称振华海科)通过将一个销售订单号贯穿于合同、设计工艺、生产、采购、检验、发货、服务、成本等全面的业务管理过程,收集全过程的管理信息数据,实现该公司与客户对订单全过程进行双向追溯。严格控制合同进程,提高合同效率;规范业务处理流程,提高产品合格率;外购价格管控,精细化成本核算。
二、总体规划
振华海科围绕“制造云平台一体化管控”模式构建数字化工厂的信息化发展目标,以纵向贯穿运营层、执行层、设备层业务数据流为手段,以数据智能驱动工厂制造任务执行的应用场景设定,加速实践制造业务流程数据化。振华海科着力实现从统一建设全局性信息系统到持续提升整合信息系统的跨越,以实现智能制造为核心,在研发设计(PLM/PDM)、生产控制(MES)、BI决策支持、购销经营平台化、制造服务网络化方面加强应用;积极推进企业在数字化、网络化、智能化方面应用,在数据应用技术、流程管控和优化创新上加强两化融合。
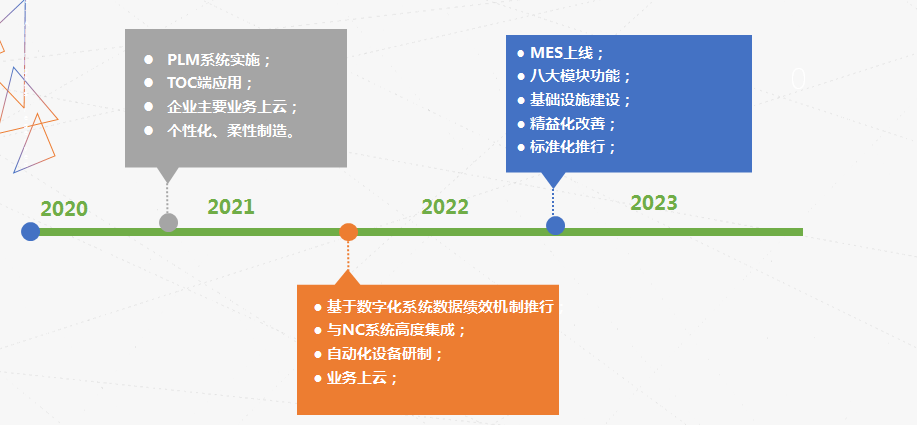
图2 时间路线图
企业以数据为中心,做到纵向、横向和端到端的集成,实现技术工艺数字化、生产物流数字化、生产制造数字化、决策依据数字化四位一体的制造过程控制管理,涵盖从技术工艺、生产排程、计划物控、材料仓库、生产制造、产品装配、成品仓库的整个生产制造过程,实现生产调度数字化、生产文档无纸化、生产数据可视化、生产过程透明化、生产决策实时化,从而提高生产效率、控制产品质量、降低生产成本。
三、具体举措
振华海科建立数字化工厂,主要目标和任务包括:购置数控加工设备、自动化辅助设备、船用闭式测试台,通过数字化工厂的打造、柔性化制造规划和生产系统的引入、数字化生产模式建立以及不断追求卓越管理理念。落实公司“数字化制造”战略,打造“数字化工厂”构建企业互联网化集成管理平台,精益产品开发设计、生产、管理,实现多种、小批量、多批次滚动产出和交付,建设工程中心、管理中心、企业级数据中心,实现制造过程“按单生产、一号跟踪”管理模式。制造工程数据管理、制造过程BOM结构管理,构建数字化生产管理平台,实现生产过程的自动化、柔性化、数字化;构建全面的业务安全监控体系,提高公司运营管理效率。
一是对机房实施改造。包括机房环境建设、更新硬件服务器、网络安全管理软件、应用软件的正版化、全网络防病毒软件五方面建设,机房环境实施改造保障了数字化系统安全稳定运行,提高了软件系统的运行效率。
二是完成PDM、CAPP、APS、DNC与NC系统的集成。延伸和拓展企业信息化系统的深度应用,避免形成信息孤岛、实现数据互联互通,建立集团化的信息管理平台,为BI决策系统提供充足的数据。
三是实施数字化工厂智能改造。购买DNC管理系统,增加接口与NC系统信息共享,实现设备的互联互通、三维及技术资料到设备的直接传输。建立满足公司战略需求的智能化车间信息管理平台(试点),开发船用泵闭式综合测试系统,实现管理与生产的自动控制和决策。
四是建立了“按单生产,一号跟踪”的先进管理平台。集合PDM、工艺管理、条码管理系统、APS排程系统、生产监控系统、质量控制系统、客户管理系统的综合功能,一个批次号贯穿合同、设计工艺、生产、采购、检验、发货、服务、成本全面的业务管理过程,实现全过程的管理信息数据集中管理,方便公司与客户对订单全过程的双向跟踪管控。
五是与泛微公司合作,建设具有开放性、严密性和实用性的办公自动化系统及移动平台。使企业内部人员方便快捷地收集处理信息,高效地协同工作;实现及时、全方位的信息共享,为企业的管理和决策提供科学的依据。
六是建设购销经营平台。公司建有企业网站、阿里巴巴经营网站平台,定期收集客户信息。利用电商平台快速而透明化的交易运作,全面推广,实现企业内部供需业务的整合、改善及优化,优化企业线上线下资源,实现线上线下产供销一体化。
七是与用友公司合作实施信息化系统的二次开发和提升。开发单品+条码管理系统、价格控制模块、质量追溯系统、生产进度管理系统、移动终端接口与触摸屏系统、合同管理系统、委外订单管理系统、BI决策系统、成本还原系统以及产品批次成本核算系统,进一步提高公司沟通和快速响应的能力,规范业务流程,实现企业精细化管理。
通过企业统筹规划,实现信息系统高度集成,推动企业数字化、网络化、智能化转型升级,基于智能制造实现的数字化工厂建设,使得企业的各项业务和管理活动规范化、标准化,更好地满足企业发展需求,带动整个水泵行业制造业管理创新和转型发展,具有示范和借鉴意义。
四、工作成效
一是有效推动战略落地。两化融合管理体系强调体系化的战略目标,过去公司战略更多体现在企业发展愿景及方向上,没有形成可测量的指标体系进行考核,无法战略落地。通过两化融合贯标,梳理公司战略并形成体系化的指标,从公司战略目标层层往下分解,通过战略分析从订单全过程跟踪管控各项指标,形成阶段性战略目标落地,公司战略真正得到了落实。
二是推进流程优化和效率提升。通过业务流程优化及组织职责调整,使得舰船用泵产品的订单全过程跟踪管控能力得到很大提升,财务成本能够根据批次核算,为财务成本细化提供科学依据。以智能制造为核心,通过后续二次开发,打通全过程数据通道,实现企业内部管理的业务流程优化、业务处理的电子化和信息化,保证业务信息的及时、准确收集和传递、为客户选型、精益生产、质量追溯、三包服务提供准确及时的各类业务动态经营信息,便于及时调控和业务决策,使得企业资源配置更加合理,便于双向过程质量追溯、进度管控、服务跟踪。获得更大的市场占有率和经济效益。
三是提高数据开发利用价值。通过NC系统的集成开发和深化应用,在实现系统数据标准化、结构化的基础上进行集成和共享,通过数据深度挖掘达到及时、有效进行业务分析和监控,以及科学决策的目的。通过有效的数据开发利用,提高了公司市场反应速度、管理效率和生产效率,增强了市场综合竞争力,同时也提高了企业的经济效益。数据的开发利用为管理者提供量化的决策依据,及时掌握生产现场进度。
该企业数据开发利用方面得到了很大的提升,对数据开发进行专门的识别分析和管理,发掘了数据背后的价值,并将分析结果用于指导管理改进。相关成效数据如下:
通过信息和数据集成,提高生产订单管控能力和生产效率,产能提升20%,生产订单按时完成率从90.3%提高到90.6%;提升产品质量,成品一次交验合格率从91.96%提高到92.3%;实现从零件到部件到产品的追踪查询,也可以实现从产品、部件到零件的追溯查询,满足了海军产品追溯性需求,产品可追溯率达到100%;新产品研发周期从253天缩短了250天;三年累计新增销售28413万元,利润7560万元,税收4560万元;半成品库存减少2566万元;企业流动资金运转周期从86天提高到42天。